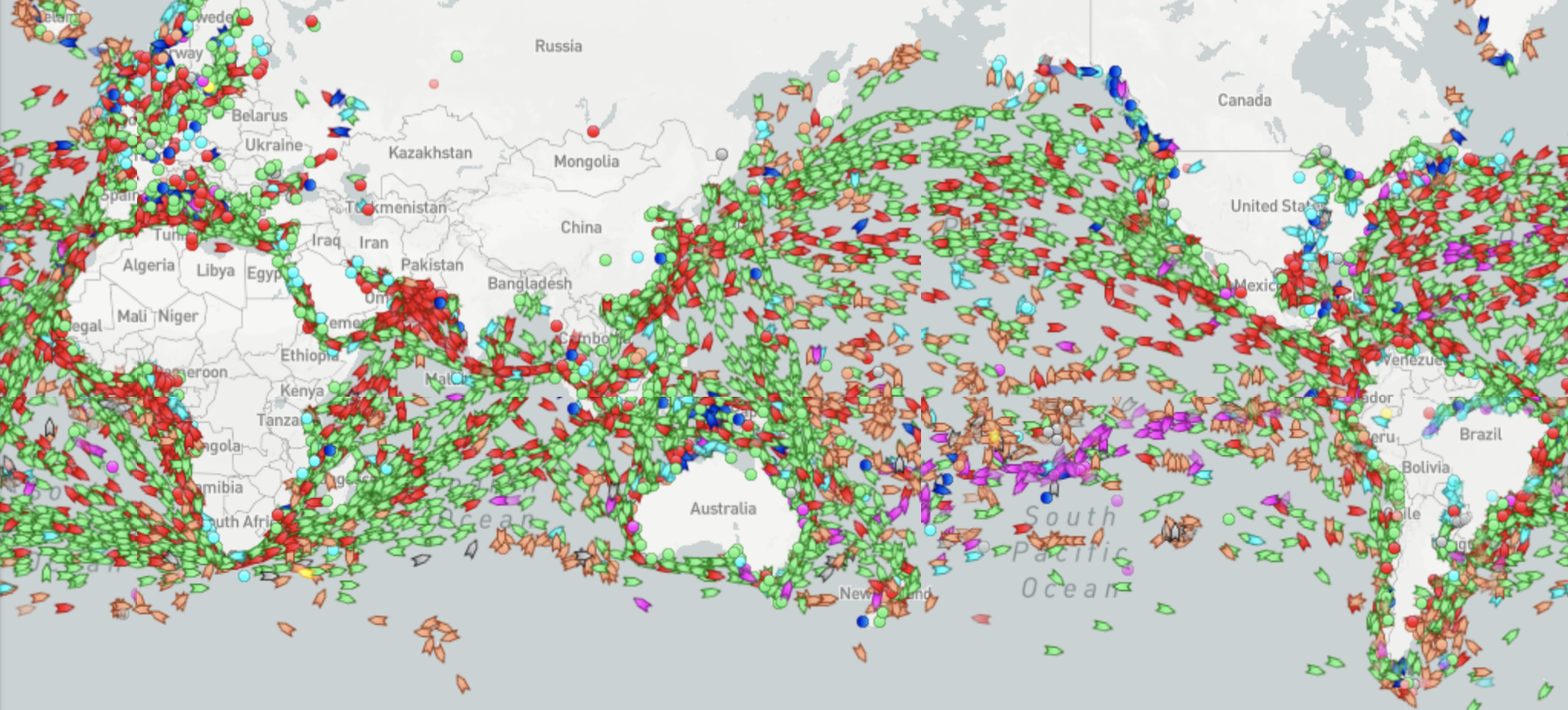
A little over four years ago, the Trump administration placed a 25 percent tariff on imports from China, including cars, hard disks, and aircraft parts. China hit back with 25 percent tariffs on U.S. agricultural products. The resulting U.S.-China trade war threw global supply chains into chaos. COVID-19 brought a whole new set of challenges, and now we have the Ukraine crisis and China lockdowns complicating matters further still.
Prior to the trade war, supply chain professionals enjoyed a long period of relative stability. We could optimize the supply chain once a quarter, or maybe once a month, and let it run. When the trade war happened, it seemed like a discrete event. We would simply recalibrate and restabilize. Instead, it’s been one upheaval after another.
It’s unlikely that we are going to return to a time when we can simply fix it and let it run. We have to change the way we do things. We have an increasing amount of data at our disposal. We need people, processes, and technology that can help us analyze it and adapt to the constantly changing environment—ideally in real time.
Chasing Imperfect Hypotheses
When it comes to managing supply chains, most companies rely on lots of internal and external data sources to predict what they’ll need months ahead of time in order to fulfill future orders. We’re always chasing an imperfect hypothesis, with new data coming in all the time. We’re constantly updating what’s in the warehouse and what’s coming in from suppliers against ever-shifting demand. It never stops.
ERP systems are not designed for the type of constant analysis and readjustment required. Purpose-built supply chain planning and management systems typically cost millions of dollars, take more than a year to implement, and once in place are relatively inflexible.
Even with these systems in place, in order to bring all the data together, many organizations have to create and maintain some bespoke internal system—typically a monster Excel master spreadsheet—to be able to keep recalculating and reanalyzing their data. As painful as this is, it was workable for a while, as long as supply chains remained stable.
Working Nights and Weekends
That was the case for the first couple decades of the 21st century. Companies in the developed world spent time and money building relationships overseas that could offer both low-cost production and just-in-time delivery of goods. Developing countries competed for that business because it bolstered their economies. There was an efficient market that was relatively predictable.
When the trade war hit in 2018, the cost benefits of manufacturing in China suddenly vanished. Companies scrambled to adjust. At the company where I was working at the time, we created a war room of team members who worked nights and weekends updating our monster Excel spreadsheet to analyze impacts and alternatives across tens of thousands of products in our global supply chain.
Then in 2020 the pandemic hit. All of sudden, the entire global supply chain was turned upside down. And now we have the war devastating Ukraine, a major producer of grain, potatoes, and sunflower oil. And we have sanctions on Russia, both official and unofficial. When a company such as Starbucks or McDonalds pulls out of a country as big as Russia, the reverberations are felt in supply chains across the globe.
Planning in Shorter Increments
You can see why “reoptimize and let it be for a while” is not good enough anymore. We need tools to be able to continually pull in accurate real-time data and reanalyze it as changes happen. Doing this kind of work in Excel is not sustainable.
Right now, companies are looking at legacy supply chain tools to try to solve the problem. But not only are they costly to buy and slow to implement, the minute you get a curveball, you have to reprogram the system. With the scope and pace of change we’re seeing, your implementation could be out of date before it even launches. Forget about trying to turn on a dime to respond to some catastrophic event.
As organizations digitize, more internal data, and external data from ports, customs offices, shipping companies, etc., is becoming available and closer to real time every day, but it’s all in different formats. Being able to pull in these different data sources into a modern analytics platform could help solve the problem in better ways.
We implemented Incorta at the company where I was working when the trade war started because it happens to be better than most supply chain tools for the needs of today. It’s quick to implement, and it’s easy to change and easy to pull in new, disparate data sources. It’s nimble enough to allow organizations to navigate through profound changes in the supply chain. And you don’t need to be a rocket scientist to use it.
Having the right tool is part of the puzzle. Then you need the right people and processes in place to use the tool effectively.
Optimizing for Change
There is no crystal ball we can look at to predict the future, and no magic wand we can wave to fix the turmoil in the global supply chain today. Something that complex, dynamic, and interconnected doesn’t lend itself to simple solutions.
What we have to do is recognize that we are living through a period of great change. It’s likely that we will experience still more external shocks that will cause us to have to break supply chains apart and reassemble them yet again. What we have to optimize for is the ability to change. Having the tools, people, and processes to be able to do that quickly and in much bigger ways is going to be the only way to thrive.
Ready to see how Incorta can help? Spin up a free trial or register for an upcoming Virtual Hands-On Lab to learn more.