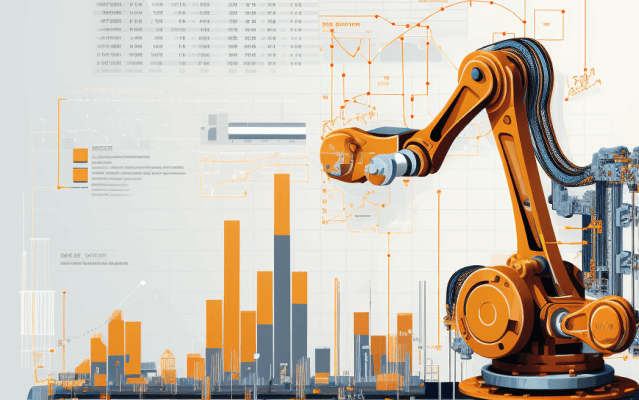
In today’s digital age, the fusion of big data and industry 4.0 is not just a buzzword, but a transformative force. These technology organizations are reshaping industries, making them smarter, more efficient, and different. But what exactly happens when big data meets Industry 4.0? Stick with us and let’s dive deeper into this!
The essence of big data
The term big data refers to large and complex data sets that are rapidly expanding, are difficult to process and analyze data using traditional methods.
This data can be structured, like traditional databases, or unstructured, like text, images, or videos. With the high rate of data being produced, these sets, when utilized properly, have the potential to provide profound insights that can help optimize processes, predict trends, develop new products, and improve decision-making.
Various companies from different industries have been adopting a data-driven culture, and the manufacturing sector is no exception. The Gemba (shop floor) produces a lot of meaningful data, and when managed correctly, a company can develop predictive work through Kaizens and achieve significant savings.
When we talk about big data and manufacturing together, the term “Industry 4.0” comes up. With that said, let’s learn more about this term.
Understanding industry 4.0
Industry 4.0, also known as the fourth industrial revolution, refers to the increasing digitization and interconnection of processes, systems, and objects in industrial production.
Based on a combination of technologies such as the Internet of Things (IoT), Artificial Intelligence, advanced robotics, and the analysis of large volumes of data (big data), this revolution aims to create manufacturing systems that are more efficient, flexible, and autonomous.
The main characteristic of Industry 4.0 is the fusion of the digital world with the physical world, enabling machines and people to communicate in real time, optimize systems and adapt to product and market changes and requirements meet.
One of the pillars of Industry 4.0 is the ability to collect and analyze large amounts of data. With sensors installed on devices and equipment, their condition and performance can be continuously monitored.
For example, predictive maintenance is when anomalies can be detected before they cause failure, reduce unexpected downtime, and maximize efficiency.
Additionally, data analytics enable companies to better understand market trends, adapt more quickly to new demands, and adapt to customer needs.
Big data and industry 4.0 working together
As mentioned above, Big Data and Industry 4.0 are partners. Working together, you can achieve optimization and potential savings:
- Predictive maintenance: With the help of big data, companies can predict when devices are likely to fail. Predictive maintenance instead of traditional routine inspections allows for timely intervention, saving time and money.
- Advanced supply chain management: Big data provides a comprehensive view of market trends, allowing companies to adjust their supply chains in real time. Combining Industry 4.0 tools means that this transformation is faster, more efficient and more accurate.
- Real-time decision making: From production integration to inventory management, it delivers real-time analytics through a combination of big data and Industry 4.0, making instant decision-making not only possible, and rather it is a new process.
- Customized customer experience: With big data insights, businesses can tailor products and services to each customer’s unique needs. When mixed with the automation capabilities of Industry 4.0, this personalization occurs at unparalleled scale and speed.
The challenges of integrating big data into Industry 4.0
Skills, time and security are just a few of the challenges you will face when implementing this new approach for your organization.
Working with big data means that ERP and machine data are available for processing and analysis. Depending on the technology stack you use, this process can be expensive.
You need solutions that integrate quickly with these systems and make it easy to transform data sets, run data analytics, and create intuitive dashboards That’s where Incorta steps in.
We have helped manufacturers optimize their processes with our data apps. Companies using Oracle EBS, BlackLine, SAP, and Salesforce are adopting Incorta to improve their productivity.
PlayPower, the world’s largest manufacturer of commercial playground and entertainment equipment, has embarked on a journey to digitally transform detailed financial analytics across its many ERPs, brands and business units.
PlayPower used Incorta to consolidate its financial information from 15 source databases into a single data warehouse.
These strategic decisions resulted in a 30% reduction in manual processes, and a 40% increase in the efficiency and cost of aggregate corporate finance.
You’re welcome to watch our webinar and learn more about Incorta for manufacturing: Deliver 40% Increase in Efficiencies in Manufacturing with Incorta.
Conclusion
The combination of big data and Industry 4.0 is more than just a technological breakthrough—it’s the backbone of future smart jobs.
While there are challenges, the potential benefits far outweigh them. Companies looking to transform, invest and nurture will surely take advantage of the invaluable advantages of this dynamic duo.